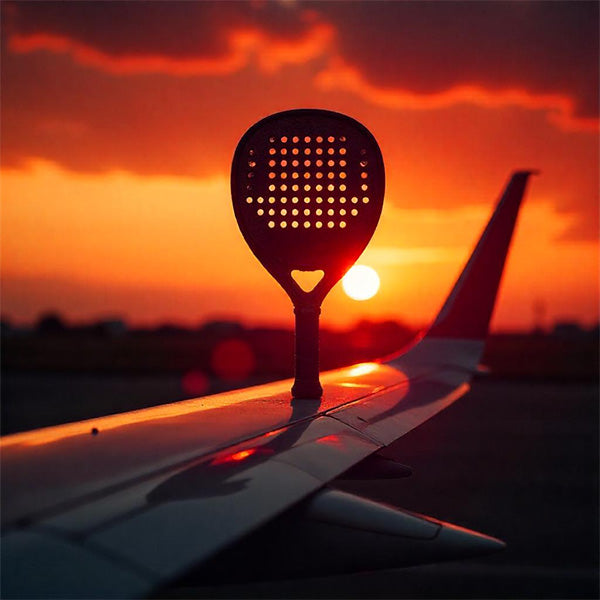
What do a padel racket and an airplane wing have in common? More than you might think!
t may sound exaggerated, but it’s not. Although they may not seem alike at first glance, the manufacturing process of a mid- to high-end padel racket has surprising similarities with one of the most sophisticated structures in modern engineering: the wing of an airplane.
1. Use of advanced composite materials
In both aerospace and sports, composite materials like carbon fiber and fiberglass play a starring role.
In airplane wings, these materials are essential due to their high strength, low weight, and ability to withstand enormous loads without deforming.
In padel rackets, they provide lightness, striking power, control, and durability—key qualities for good performance on the court.
2. Molding process: precision in three dimensions
Both products require molds to achieve their final shape:
In aerospace, the process can include techniques such as resin transfer molding (RTM) or automated fiber placement (AFP).
In the manufacturing of padel rackets, layers of resin-impregnated fiber are placed into a closed mold that is then cured under heat and pressure.
3. Layered construction (lamination)
In both cases, overlapping layers are the key to strength and performance.
Wings are laminated with multiple layers to form both the "skin" and internal structural elements (spars and ribs).
In rackets, several layers of fiber (carbon or glass) are placed around a core, with different orientations to fine-tune stiffness, power, or control.
4. The core: the heart of performance
The core is fundamental in both, though with different purposes:
In padel rackets, EVA rubber or FOAM is used to absorb impacts and provide comfort.
In airplane wings, sandwich-type structures may use rigid foam or honeycomb cores, which increase stiffness without adding weight.
5. Curing process: where everything solidifies
The resin that bonds the composite together needs a thermal curing process:
In aviation, this is done in autoclaves under high pressure and temperature to achieve maximum strength.
In padel rackets, ovens or thermal presses are also used to fix the shape and solidify the structure.
6. Dynamic and aerodynamic design
For an airplane, aerodynamics are everything: less air resistance and more lift.
In a racket—although it doesn’t fly—the design affects swing speed and maneuverability. Details like the racket’s throat or drill pattern help reduce air resistance.
7. Finishing and quality control
In both processes, surface finishing (sanding, painting, priming) is not just aesthetic; it also protects and ensures durability.
And of course, no product hits the market without quality control. In the aerospace industry, it’s extremely rigorous. In padel, while simpler, visual and dimensional inspections are also carried out to ensure product quality.